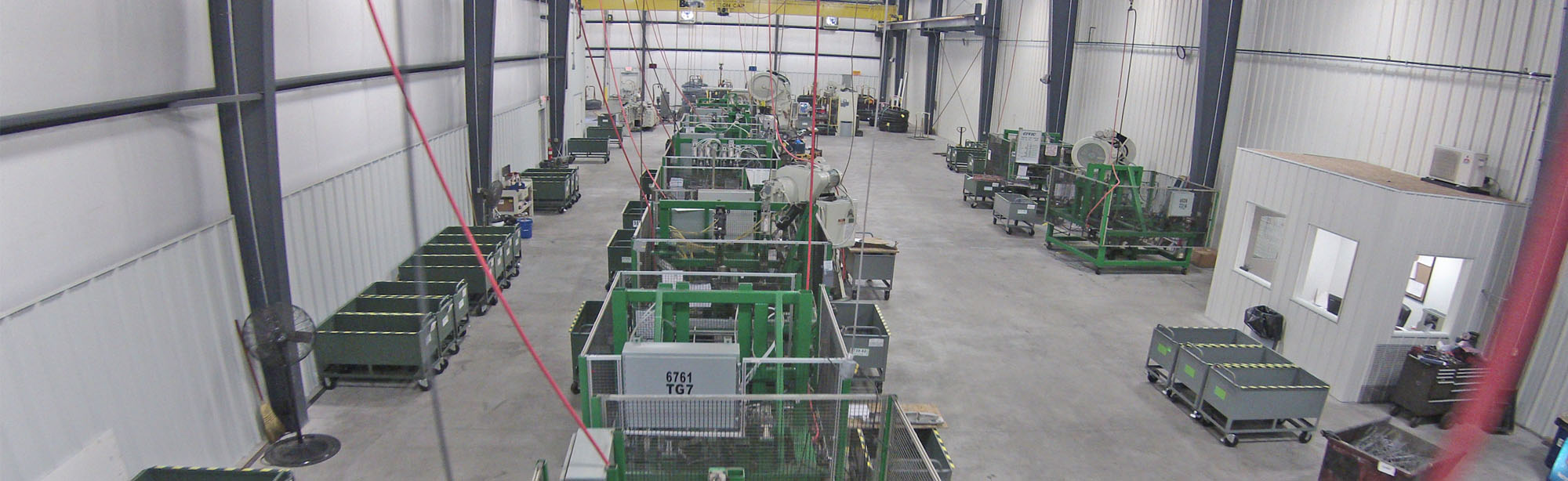
Services
Electro-Coating
E-coating is an exceptional painting choice for any steel part that requires high quality and exceptional durability. E-coating is especially valuable for oddly shaped and complex products. It conforms to multifaceted parts and maintains designed specifications of coating thickness without runs or drips. This is especially valuable for coating the inside surfaces of parts, deep recesses, weld marks and fasteners. More parts within spec translate to less waste, as well.
How it works
After completing the pre-treatment steps, the parts are conveyed to the e-coating bath area. Electric current is sent through the parts as they are dipped in the e-coating bath. This current attracts the paint that is suspended in the solution. Every uncoated area of the part attracts paint until the coating is uniform across the parts surface.
After e-coating, the part is rinsed to remove any excess paint. The rinsed off materials are returned to the e-coating bath making e-coating an environmentally friendly process. The parts are cured in a high-temperature oven following the rinse. This hardens the paint for a smooth and continuous finish.
Powder Coating
Always over e-coating
Because H.E. Orr operates with e-coating and powder coating on the same production line, every part gets e-coated prior to being powder coated. This provides companies an extra level of protection for their parts and is a highly desirable benefit to improve the corrosion protection attributes of the paint.
Powder coating is considerably more durable than liquid paints providing longer corrosion protection to extend the useful life of coated parts. Powder coated surfaces are also much more resistant to chipping, scratching, and damage in general because the finish is thicker and oven cured. It is also more resistant to natural fade and wear. It is a uniform coating that has virtually no inconsistency along a parts surface or from one part to the next. Powder coating leaves a smooth finish with no runs, drips, or sags.
How it works
After completing the pre-treatment and e-coating steps, the parts are conveyed to the powder coating booth. The process is similar to e-coating except that the powder is dry and it is sprayed on to the parts. The parts are charged via electric current and the powder carries the opposite charge. Like e-coating, the powder coating material is attracted to the part in a uniform fashion. The parts are again oven cured for hardness and a smooth finish. Excess powder is reclaimed and recycled, reducing waste and protecting the environment.
Wire Forming
The key to a successful wire forming operation is efficiency and precision. What matters most is getting the right products made to spec with the highest quality in the least amount of time and at the most competitive price. Although this may sound like a list of conflicting goals, finding a supplier that has these goals in mind can be a tremendous advantage to your organization.
When you use H.E. Orr for wire forming you are using a one-stop supplier that can supply your OEM parts from concept to a finished condition wire form. Orr has e-coating and powder coating not only in the same facility, but on the same production line! This, along with sub-assembly capabilities, makes Orr tough to beat for efficiency and savings. Orr runs five to six million parts through its centrally located, Paulding, Ohio, factory each year.
H. E. Orr starts with customer specifications. A careful analysis of your needs helps determine the most cost-effective way to manufacture your parts. Whether working with customer supplied drawings or directly with the customer to design the part on our CATIA or Auto CAD systems, efficiency and quality are the top goals.
Wire formed parts are manufactured either on a dedicated bender or on a series of punch presses. Orr can accommodate solid or tube steel from six to 12 mm in diameter. If the size and scope of the specified part makes a dedicated bender more cost-effective, the engineering and tooling team works with a local preferred supplier to build the equipment to specification. If the volume is smaller, a punch press and tooling system is often more cost effective. H.E. Orr is a one-stop supplier that manufactures OEM parts from concept to a finished condition wire form.
Sub-Assembly and Kitting
Sub-assembly and Kitting
When you use H.E. Orr for wire forming you are using a one-stop supplier that can supply your OEM parts from concept to a finished condition wire form. After the parts are formed, either through forging or wire forming, and coated, they often move to the sub-assembly and kitting operations. Sub assembly includes installing rubber hoses or plastic parts to the finished wire form. Orr has invested in the equipment required to install these parts quickly and efficiently. Once a part leaves our facility, it is ready for installation in your OEM environment.
Kitting involves assembling tools or other parts into a supplied package which is then shipped to your facility.
Hot Upset Forging
Forging is one of the oldest known metalworking processes. Traditionally, forging was performed by a smith using hammer. The smithy or forge has evolved over centuries to become a facility with engineered processes, production equipment, tooling, raw materials and products to meet the demands of modern industry.
Forging can produce a piece that is stronger than an equivalent cast or machined part. As the metal is shaped during the forging process, its internal grain deforms to follow the general shape of the part. As a result, the grain is continuous throughout the part, giving rise to a piece with improved strength characteristics.
Some metals may be forged cold, however steel is almost always hot forged. Production forging involves significant capital expenditure for machinery, tooling, facilities and personnel. In the case of hot forging, a high temperature furnace (sometimes referred to as the forge) will be required to heat ingots or billets. Orr’s forging operations require the use of metal-forming dies, which must be precisely machined and carefully heat treated to correctly shape the part, as well as to withstand the tremendous forces involved.
Cold Forming
Originally, cold forming was known as cold heading. Cold forming was a common way to make the heads of screws and bolts. After forming the head, the threads would be cut or rolled into the material. The advantage was the parts could be made quickly with little or no scrap.
H.E. Orr Company uses cold forming machines to make simple and complex shapes for a wide variety of applications. Orr’s tooling is designed to extrude the material to (.004″) of an inch tolerance. Then a series of punch presses shape the part to customer specifications. The number of punch presses is determined by the specifications of the parts produced.
Although cold forming is an old technology, it has evolved to produce complex parts with very desirable characteristics. Cold-formed parts have excellent strength because the material “flows” into its final form rather than being cut. Dimensional tolerances and surface finishes can be as good as machining and very cost effective when larger runs are needed.
Wire Drawing
To help reduce costs for wire formed parts, H.E. Orr buys raw materials directly from steel mills rather than in precut bars. This way there is no middle man to add an additional markup and inflate the price for finished parts.
This also allows Orr to draw the wire down to the exact specifications needed—keeping a tighter control on tolerances and quality. For example, a coil of plain carbon steel comes in at twenty-nine sixty-fourths (29/64″) of an inch, and specifications might require drawing down to 10mm with only a + or – .03125″ tolerance.
Orr’s technicians and equipment can easily meet these requirements. As part of the drawing down process the steel is straightened then cut to length and moves to the forming stage. At this point the “memory” is removed from the steel. Memory is taken out of the steel to ensure a quality finished product. H.E.
Orr Company can accommodate solid or tube steel from 6 to 12 mm in diameter. To keep pricing as competitive as possible, Orr does not stock materials. Just-in-time inventory management is used for the most cost effective delivery system. Excellent relationships established over many years in business with suppliers allow H.E. Orr to get quality materials quickly.
Design and Quality Control
A thorough analysis of customer specifications and requirements by Orr’s technical team determines the most cost-effective way to manufacture the specified parts. Whether working with customer-supplied drawings or custom engineering a design on Orr’s in-house CATIA or Auto CAD systems, efficiency and quality are paramount.
Computer Aided Design (CAD)
H.E. Orr Company utilizes the latest CAD software for the process of design and design-documentation. CAD software provides the input tools to streamline design processes; drafting, documentation and manufacturing processes.
Coordinate Measuring Machine
H.E. Orr Company utilizes a coordinate measuring machine (CMM) for measuring the physical geometrical characteristics of prototype parts. H.E. Orr uses it CMM in manufacturing to test parts against the design intent. By precisely recording the X, Y, and Z coordinates of the target, points are generated which can then be analyzed via regression algorithms for the construction of features.
Quality Control Gauge
A quality control gauge is used both in the prototyping process and throughout the run of your parts to ensure that specifications are met for the entire production run.
In-house Salt Spray Test Facility
Every product gets extensive testing to make sure that it meets customer requirements. The most common test is the Salt Spray test. Orr’s team of engineers and quality control experts will work with you to achieve the salt spray hours that your application requires.
We rigorously test parts at regular intervals to ensure that the proper coatings are being applied to specified tolerances over the days, weeks or months that your parts are running. It is this commitment to quality and testing that has earned H.E. Orr its solid reputation in the industry.
Pre-Treatment
E-Coating and Powder Coating Start With Pre-Treatment – 48 hour turnaround
Zinc Phosphate Eight-Stage Pre-Treatment for Superior Quality
One key to assuring the high quality output of H. E. Orr’s coating process is the care and attention taken to pre-treat every part. Orr utilizes an eight-stage pretreatment process that establishes an outstanding bonding surface prior to coating. To many, this sounds like more steps than needed, but customers of H. E. Orr appreciate the consistency and quality that the pre-treatment process generates.
Step 1– An alkaline cleansing solution that removes most contaminants
Step 2– A second cleanse in an alkaline solution to remove any contaminants that were not removed in step one. This insures that parts are free of anything that would impair adhesion.
Step 3– Thorough rinsing to remove any solution from the part
Step 4– Second rinse to prep for zinc phosphate activation
Step 5– Zinc phosphate coating. Orr uses non-metallic zinc phosphate, rather than cheaper iron phosphate because it is a crystalline coating that chemically adheres to the substrate. Zinc phosphate is extremely adherent providing a uniform coating with improved coating adhesion properties. It coats better in recessed areas and provides better corrosion resistance. Because of these qualities, it is the standard for the automotive industry and at H.E Orr.
Step 6– Rinse to remove any excess zinc phosphate from the parts
Step 7– Rinse again
Step 8– Water rinse in a deionizer to reduce conduction in the e-coat bath
Different coaters use different methods to pre-treat parts. Iron phosphate is a cheaper process and makes equipment easier to maintain. However, Orr’s experience demonstrates that the higher quality provided by zinc phosphate pre-treatment process is worth the effort it takes to deliver a superior quality product.
Salt Spray Testing
The coating business is all about meeting customer specifications and consistently delivering quality parts on time. Part of the process is testing to ensure that every part that comes off the line meets quality standards.
Every product gets extensive testing to make sure that it meets customer requirements. The most common test is the salt spray test. In this test, coating samples are collected on 3″ x 9″ plates. The plates are run through the coating line at the same time as customer parts. This ensures that the test plates are coated in the same manner as the parts.
The plates (with and without cross-hatching) are put in the salt spray test chamber where a concentrated salt fog is generated. This process simulates the conditions a part may be exposed to while in use, though at a severely accelerated rate. Since few things corrode like salt, the salt spray test is the industry standard. The ratings are based on the hours the plate can last in the chamber without any signs of corrosion.
Depending on the metals coated and the process used, our team of engineers, technicians and quality control experts will work with you to establish a coating system that will meet your requirements for salt spray test hours. We rigorously test parts at regular intervals to ensure that the proper coatings are being applied over the days, weeks or months that your parts are running. It is this commitment to quality and testing that has earned H.E. Orr its solid reputation in the industry.
Size and weight
H.E. Orr Company’s production line has a 4′ x 6′ window. Orr can accommodate any part that will fit in this space. Orr also has the added advantage of dual drives on the line that allow it to handle heavier parts than what many e-coaters can accept. If have been told your parts are too heavy for a particular production line, it makes sense to call H.E. Orr as we can typically handle what many coaters cannot.